Bridge Construction & Development
Building a bridge is a complex undertaking requiring knowledge and expertise. Several variables, including engineering constraints, costs, and environmental impacts come into play when deciding which construction method to use and bridge type to build.
Our value-added expertise includes 3D modelling and Virtual Design and Construction (VDC), which facilitates the decision-making process before and during construction and improves communications with all stakeholders, including local communities. The application of innovative technologies enables all stakeholders to visualize the future bridge and to embrace the proposed concept.
VDC provides our design teams with the tools they need to integrate our design models with contractor scheduling, fabrication, and the construction process. As the bridge construction industry moves towards electronic delivery of project plans, WSP is at the forefront.
Bridge construction typically involves methods using relatively discrete elements, like piles and girders, which are assembled piece by piece. Over the past 50 years, however, construction methods have evolved to reduce traffic impact, facilitate building in congested areas, reduce overall construction schedules, and improve the long-term service life of structures.
Segmental construction is one of the most important developments in construction in the last century and is a proven method for delivering durable structures that are both cost-effective and visually appealing. This construction method is used throughout the world and its versatility can be applied to most structures, including highway, rail, and even movable bridges.
Segmental construction should be considered when one or more of the following conditions exist:
The bridge is long and/or tall, and there is a potential for repetitive construction details.
Construction access is very limited and/or traffic disruptions are unacceptable.
Aesthetics play a significant role in the project
Segmental construction can reduce construction time, limit environmental impacts, minimize traffic disruption, improve seismic performance and reduce maintenance costs.
Precast vs. Cast-in-Place
Segmental concrete construction can be implemented in two ways: using precast elements or through cast-in-place construction.
The advantages offered by precast elements are mainly related to fabrication, conducted in a plant that produces more consistency in quality products and where segments can be fabricated in parallel with early field construction activities, thus improving scheduling. The main challenges involved with precast segmental construction lie in the logistics and the setup process between the casting yard and the construction site.
Alternatively, cast-in-place construction requires that a substructure be completed prior to fabrication of the superstructure. Cast-in-place segmental construction is used when precast segments are too heavy to be shipped or access to the site is too restrictive, which can occur as spans get longer or bridges get wider.
Cantilever Construction
As the industry evolved, the need for a construction method requiring no falsework became obvious. The solution: a self-supporting bridge built using the cantilever construction method. When scaffolding and other temporary supports are difficult to install, this method saves all temporary work and allows bridges to be built at great heights.
The balanced cantilever construction method is used when few spans ranging from 50 to 250m exist. Bridges using this method can be either precast or cast-in-place. Once the piers are built, they are used as an erection platform for precast segments, or to support a form traveler for cast-in-place segments.
This method is easily adaptable to irregular and long span lengths, congested project sites, rough and water terrain, rail crossings, and environmentally sensitive areas.
The cantilever method is the preferred method for building cable-stayed bridges. Once segments are installed, they’re supported by new cable-stays in each erection stage. Since no auxiliary supports are required, it is both an economical and practical solution for long cable-stayed bridges.
Incremental Launching Method
The highly-mechanized Incremental Launching Method (ILM) is typically performed in a series of increments. It is used in the construction of continuous concrete bridges as well as with steel girder bridges. The ILM can also be applied to tied-arch and truss spans, if fully assembled before launching, as well as to the construction of small and medium-sized cable-stayed bridges.
Although the ILM will never qualify as the most cost-effective method for building a bridge, it offers significant other advantages when used in the proper circumstances, such as spanning inaccessible or environmentally protected obstacles. Significant advantages of the ILM include minimal disturbance to surroundings, no falsework required, reduced area for superstructure assembly, and increased worker safety, as erection work is done from the ground.
Emerging Technology Trends in Bridge Construction
New technologies and materials are helping engineers and construction professionals build bridges better and faster, while also improving maintenance for longer bridge life. Sensors are being embedded into both new and existing bridges to provide continuous feedback on structural conditions. This data helps engineers identify and address problems earlier and improve public safety. One bridge building technology being used today is borrowing from ideas and designs of the past to produce a new structurally sound engineered bridge.
The New Technology of Bridge Design
The art of bridge design is a time-honored pursuit that, throughout the centuries, has undergone significant advances in engineering and technology as a result of mankind’s passion to conquer the challenges of any given crossing. It has evolved through the acceptance of well-established practices, codes and construction techniques. In fact, when new materials or methodologies are brought to the market, it often takes many years for the techniques to gain inclusion in the modern practice of bridge design.
For example, even after the high-strength characteristics of iron were recognized, as compared with timber, iron was still used as a lighter-weight substitute. It was years before it came to be a stand-alone structural material for bridge design. Steel also went through a similar transformation before it was used as a replacement for iron; welding and bolts replaced rivets; and in today’s modern age, computer analysis and CAD (from matrix methods though FEMs) have replaced hand calculations and hand drafting.
Where are we now in this continuum? Advanced modeling techniques, material choices and analysis methodologies adopted for building practices are not yet fully embraced within the bridge industry. This paradigm will soon shift, and we anticipate that advanced computational modeling will be one of the next big advances in bridge design.
Modern steel bridges taking advantage of the latest advances in automated fabrication and construction techniques are able to provide economic solutions to the demands of safety, rapid construction, aesthetics, shallow construction depth, minimal maintenance and flexibility in future use. Steel also scores well on all the sustainability measures, and offers a broad range of benefits addressing the economic, environmental, and social priorities of the ‘triple bottom line’ of sustainability.
Beam bridges
A beam and slab, or composite bridge is one where a reinforced concrete deck slab sits on top of steel I-beams, and acts compositely with them in bending. There are two principal forms of this beam and slab construction; multi-girder construction and ladder deck construction. Between them, they account for the majority of medium span highway bridges currently being built in the UK, and are suitable for spans ranging from 13m up to 100m. The choice between the two forms depends on economic considerations and site-specific factors such as form of intermediate supports and access for construction.
Box girder bridges
Box girders comprise two webs that are joined top and bottom by a common flange creating a closed cell that offers very good torsional stiffness, which may be required on highly curved bridges. In beam and slab bridges, box girders are an alternative to plate girders at the upper end of the span range, where they offer a lower steel weight, although this has to be balanced against increased fabrication costs. Such composite box girder decks may take the form of multiple closed steel boxes, with the deck slab over the top, or an open top trapezoidal box, closed by the deck slab.
Longer spans of 100 to 200m typically use either a single box or a pair of boxes with crossbeams. For such long spans and for bridges such as lifting bridges, where minimizing structural weight is very important, an all-steel orthotropic deck may be used instead of a reinforced concrete slab. Above about 200m, box girders are likely to be part of a cable-stayed bridge or a suspension bridge, where they are specially shaped for optimum aerodynamic performance.
Our Co-Engineering Partner’s technology:
BERD | ONE BRIDGE, ON E SOLUTION
EXCLUSIVE TECHNOLOGY. EQUIPMENT FOR IN PLACE CONSTRUCTION OF BRIDGES AND VIADUCTS DECKS, SPAN BY SPAN, WITH LARGE SPANS (SPAN LENGTH BETWEEN 70 AND 100 METRES – BETWEEN 229 TO 393 FT.).
PRECAST SEGMENTS LAUNCHING GANTRY FOR THE CONSTRUCTION OF BRIDGES AND VIADUCTS WITH LARGE SPANS (BETWEEN 70 AND 120 METRES – BETWEEN 229 TO 393 FT.), SPAN BY SPAN.
EQUIPMENT FOR CONCRETE CASTING OF INPLACE SEGMENTS USING BALANCED CANTILEVER METHOD.
CM (CANTILEVER MACHINE EQUIPMENT FOR BOX SECTION DECK WINGS IN PLACE CONSTRUCTION, WITH OR WITHOUT STRUTS.
EQUIPMENT FOR IN SITU CONSTRUCTION OF BRIDGES AND VIADUCTS, ABLE TO PERFORM TWO TASKS AT ONCE. FRONT SPAN: CONSTRUCTION OF THE DECKS MAIN BEAMS; REAR SPAN: PLACEMENT OF PRECAST SLAB ON PREVIOUSLY CONCRETED BEAMS AND SUBSEQUENT FINAL CASTING OF UPPER SLAB.CM (CANTILEVER MACHINE)
WE CREATE TAILOR-MADE SOLUTIONS ADJUSTED TO EACH PROJECT AND EACH CLIENT.
ALL OUR PRODUCTS AND SERVICES ARE ENABLED BY SYNERGIES BETWEEN STRUCTURES’ ENGINEERING, AUTOMATION AND R&D.
WE ARE CONSTANTLY LOOKING TO BE CHALLENGED, LEADING US TO DEVELOP STATE-OF-ART EQUIPMENT FOR BRIDGE CONSTRUCTION.
CHALLENGE US. WE’LL HAVE THE SOLUTION!




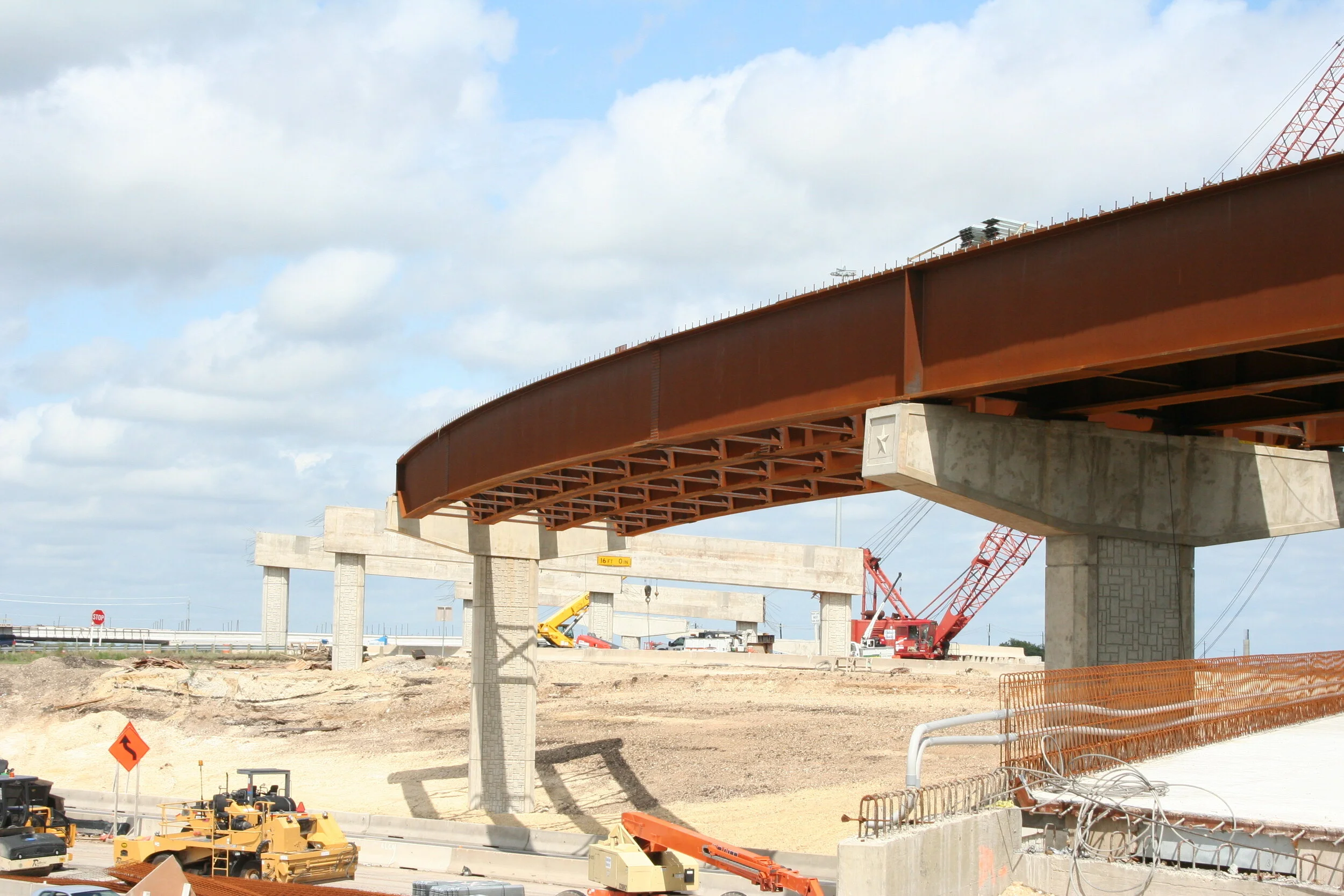